Unique technology that realizes highly difficult presses
Creating added value
core values01
Nippa's stamping
At Nippa, we own numerous unique techniques for press processing, and we handle everything from manufacturing to post-processing of essential components in various fields such as automotive-related industries.
What is stamping?
This is a processing method where pressure is applied using a press machine and make a shape(also known as metal press processing), The metal which is the material is forcefully pressed onto a mold, deforming it and finishing it into the desired shape. At Nippa, we own many transfer presses and progressive presses.
Main products
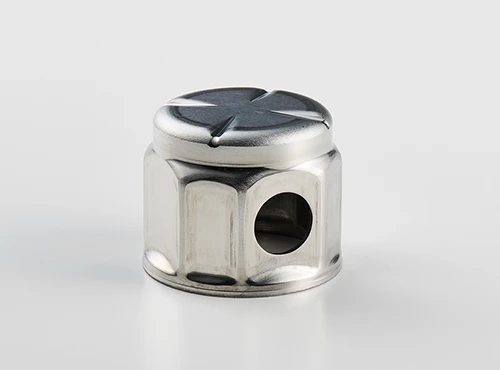
01Hausing supply pump housing
Housing Supply pump housing is used as a component part of a direct injection high-pressure pump.
The direct injection high-pressure pump is driven by the engine cam and is utilized as a component to control the discharge amount during the opening timing of the solenoid valve.
This is one of the crucial components in gasoline-powered vehicles that perform “intake, adjustment, compression” and convert it into low-pressure fuel before being discharged.
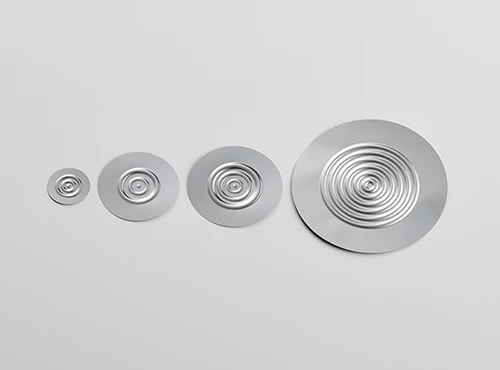
02Diaphragrm sensors
Diaphragm sensors are used as components of high-pressure sensors.
It is an important component that detects changes in internal pressure due to thermal expansion.
High-pressure sensors are used in various parts of automotive parts, such as air conditioners, exhaust pressure sensors, engine fuel pressure, and brakes.
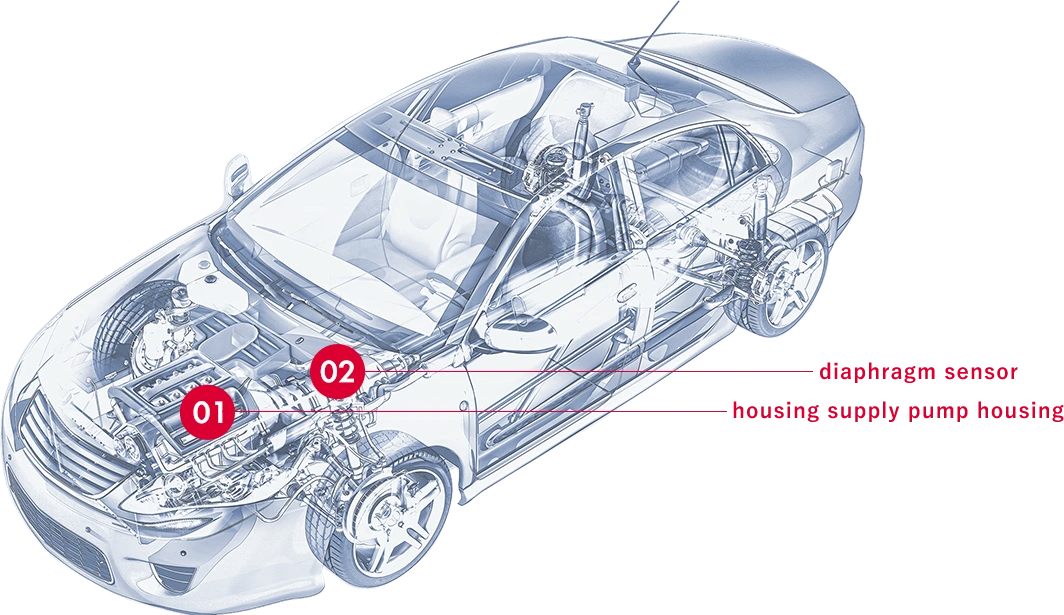
At Nippa, we are advancing various technologies in the field of stamping press processing, and providing added value to our customers by continuously refining our technical capabilities that surpass those of other companies such as pursuing high precision, molding difficult-to-process materials, improvement of ultra thin SUS processing technology, and other advancements.
Evolution of press technology
Since 1946, Nippa has been dedicated to the manufacturing of automotive components. we have diversified into various fields, leveraging the expertise in stamping know-how that we have cultivated over the years. We strive to deliver products that earn the trust of our customers. Additionally, we have established overseas bases to facilitate local production.
Install in various vehicles
Many customers have selected the insert molded parts manufactured by our company.
2 wheels
4 wheels
Large vehicle
Agricultural construction machinery
Other EVs
Beer barrelcap
Ship
Electric appliances
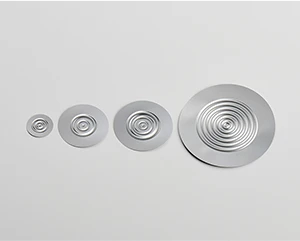
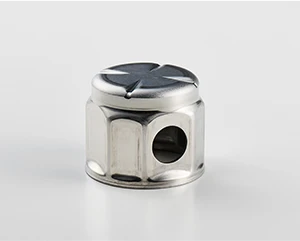
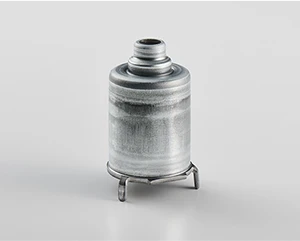
Nippa's stamping4 strengths
Integrated production system
Because we conduct integrated production in-house, we can easily respond to customer request from the time of receiving orders, and by completing everything in one company, we can achieve quick delivery through smooth communication. In order to achieve the integration of all processes within one company, Nippa also focuses on pursuing know-how in subsequent processes.
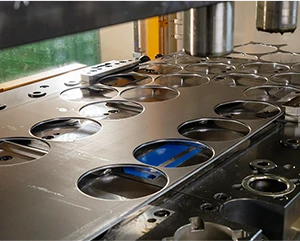
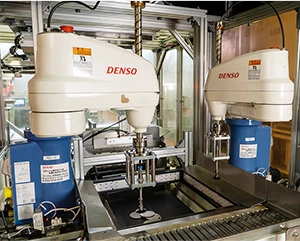
Automatic blank plate loading machine.
We perform high-yield multi-row cutting and achieve high productivity by using an automatic blank plate loading machine.
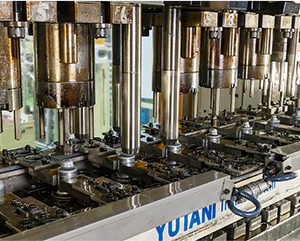
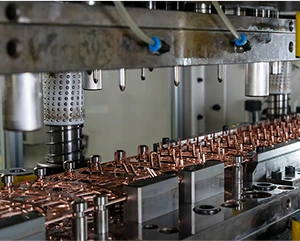
Stamping
We have facilities equipped with progressive presses, transfer presses, and MIMS, tailored to the features of the products and capable of meeting customer needs.
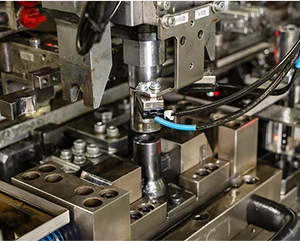
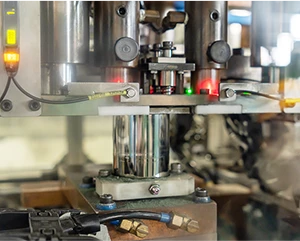
Post-processing
We have installed automatic equipment to realize products with horizontal cuts around the entire circumference and automatic equipment to perform bolt welding.
By realizing a line concept that meets various product requirements, we have achieved a short delivery time that can meet customer needs.
Development of original equipment MIMS Press LineMultiform Inline Modules
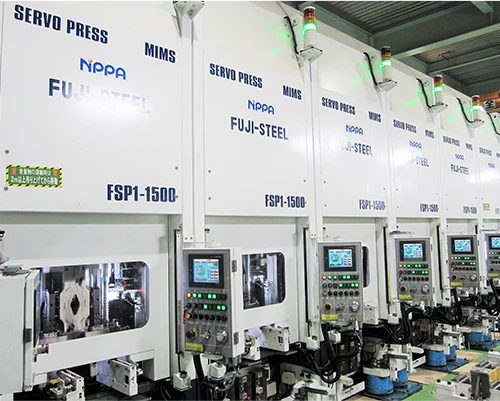
Realizing press system that is capable to handle a variety of needs and strong variations.
Conventional press selection has limitations such as press capacity, product size, and the number of processes for the product. MIMS achieves a press system that is versatile and adaptable to frequent changes, with fewer constraints for future applications.
Utilizing KARAKURI transport mechanism based on vertical motion of the press in the conveying mechanism to increase processing speed and improve productivity.
precision press
We process ultra-thin materials (20~30μm) of special SUS that are typically difficult to process using our proprietary technology, achieving high-precision corrugated molding without the use of processing oil. We ensure the integrity of all products with automatic inspection using He-leak testing, guaranteeing detection of even the smallest leaks.
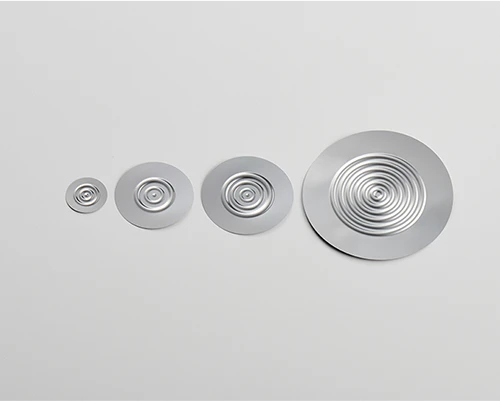
Press
High-precision molding using proprietary technology
Tray alignment
Automated alignment of Discharged product from press into tray
Leak inspection
High-precision inspection using HE
Visual inspection
All item inspection for scratches and dents of approximately 2 μm
-
Press
-
Tray alignment
-
Leak inspection
-
Visual inspection
On-site capabilities

On-site motto “Process monitoring not to create defects”
We engage in ‘thorough observation activities' as part of our quality improvement efforts. By closely examining the products, we will detect the signs of defects before they occur.
Through sharing know-how and gained through problem-solving and improvement activities across departmental boundaries, we aim to achieve a synergistic effect and further enhance on-site capabilities.
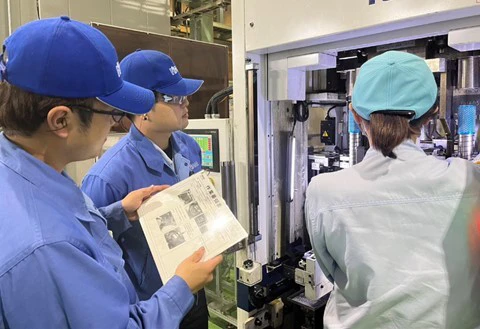
A workplace where young people play an active role: “Craftmanship is human resource development”
Young employees are playing an active role on the front lines by standardizing Kankotsu work (A work that depends on intuition of a worker that based on long experience) so the know-how of experienced employees is passed on to younger employees.