Know-how of complex multi-layer insert shape products.
Automation technology
core values02
Nippa’s insert molding
At Nippa, we own insert molding technology from resin to molding parts in order to consistently manufacture various mobility parts in-house
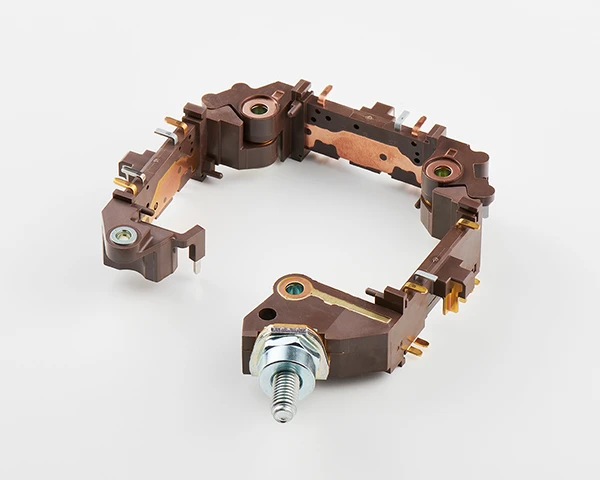
What is insert molding?
This is a technology that integrally molds insert parts (metal parts) and resin.
Nippa possesses the technology to fully automatically mold insert parts with complex shapes.
Main products
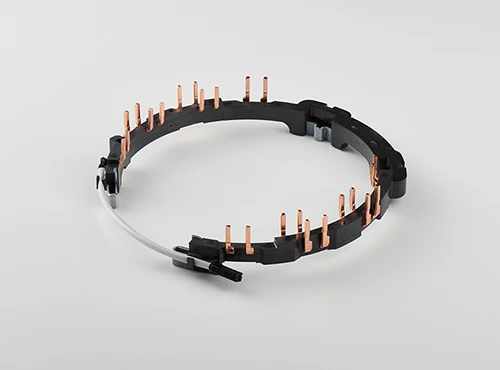
MG crossing line
This is a connecting part for constituting the wiring circuit of the stator in the MG (motor generator).
※Parts such as busbars are insulated and molded.
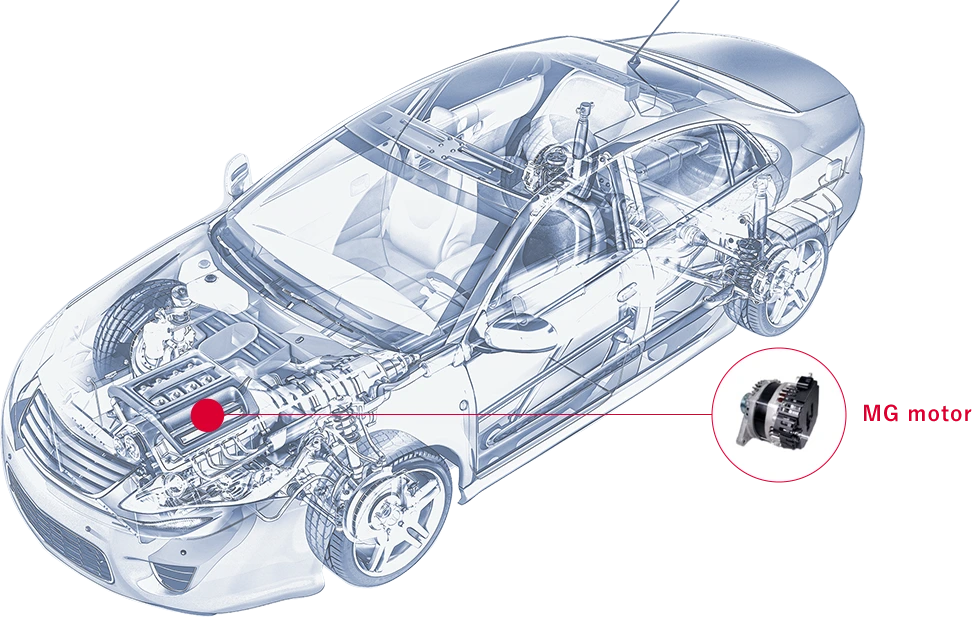
While the insert molding technology is well-known in the manufacturing industry, Nippa distinguishes itself by actively tackling the automation of complex shaped with multiple parts. The unique development capabilities of our skilled technical team, backed by abundant know-how, enabling us to enhance efficiency and precision and deliver high-quality products with cost-effective performance to our customers.
Evolution of insert molding
Nippa started producing insert molded products in 1990 and is currently performing automatic processing of insert molded products using up to 18 parts.
Install in various vehicles
Many customers have selected the insert molded parts manufactured by our company.
4wheels
Large vehicle
Agricultural construction machinery
Other EVs
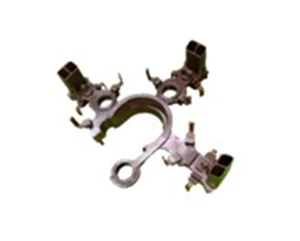
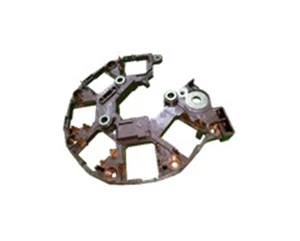
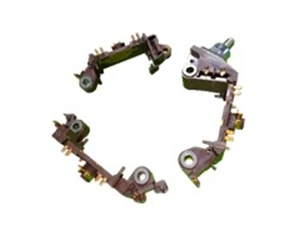
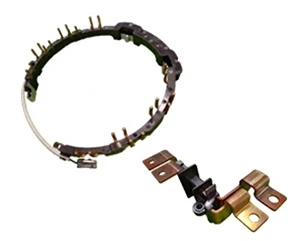
Nippa's insert molding4 strengths
Integrated production system
By consistently handling everything from the production, processing of insert parts, insert molding, to inspection in-house, it enables efficient and smart manufacturing without waste.
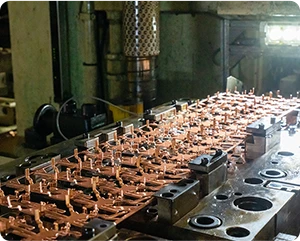
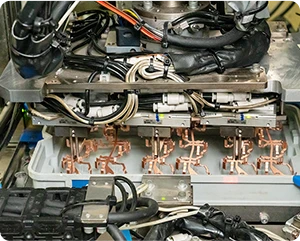
Stamping
Insert parts such as busbars are produced in-house using stamping technology.
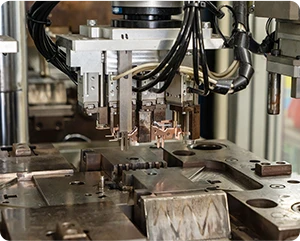
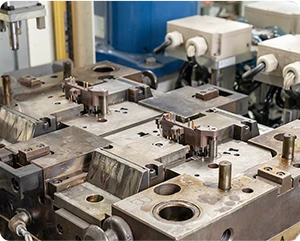
Automatic insert molding
Complex insert parts are automatically stably supplied to molding molds using slide molds.
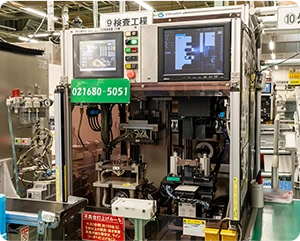
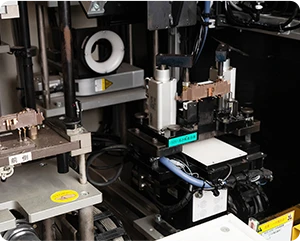
Inspection
By developing our own inspection system that meets the requirements of our products, we are able to guarantee all of our products.
- Burr inspection
- Insulation inspection
- Resistance inspection
Automation technology
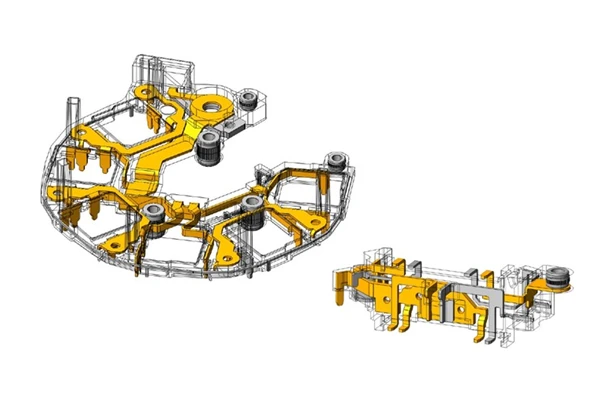
Automated multi-layer insert geometry
Nippa's insert molded products feature intricate components arranged in multiple layers within a single product.
At Nippa, we actively take on the challenge of automating the molding of complex-shaped products that require advanced technology.
Through collaborative engineering activities with our customers, we aim not only to meet product requirements but also to propose shapes that enhance manufacturability. By leveraging automation, we achieve one-shot molding of complex multi-layered insert molded products, contributing significantly to substantial cost reductions for our customers.
Ancillary technologies that create added value
Capture of post-processes
So far, NIPPA has been contributing to reducing delivery times and overall costs by being able to consistently handle the element technologies of subsequent processes (such as welding), which were separately conducted by the customer after the delivery of molded products.
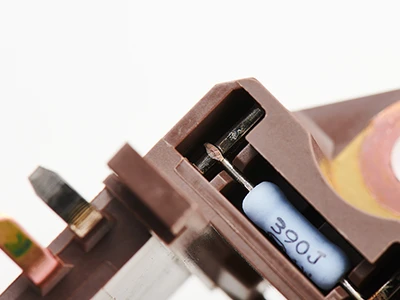
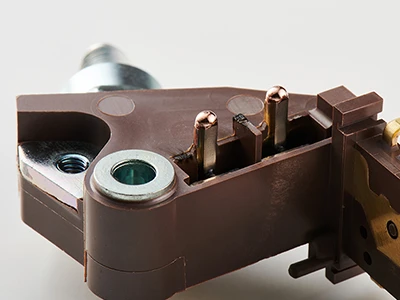
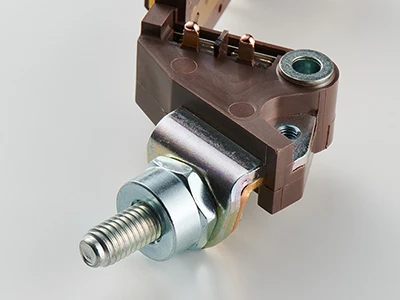
On-site capabilities
At Nippa, we believe that it is important to improve our on-site capabilities in order to make good products.
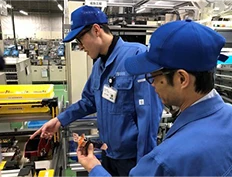
Creating our equipment collectively with everyone
Based on the experience and knowledge we have accumulated over the years, we place great importance on employees who supports the site participating since the planning stages of new equipment and encourage them to exchange opinions with engineers. In this way, the site and the engineering department will collectively embellish the equipment they envisioned in common.

Making "improvement" a "habit"
In our daily production activities, we don't settle for satisfaction with just one improvement; rather, we continually rotate and evolve the cycle of 'improvements' one after another, believing it to be the growth of both people and equipment. There are occasions where opinions may clash, but it is also where we often discover hints for further improvement. As a team, we are committed to cycling through the improvement process.