Experience and know-how of a long-established cap manufacturer
Constantly evolving automation technology
core values03
Nippa’s cap assembly
We will introduce the assembly technology of Nippa's radiator caps, which have a domestic market share of 70% and an overseas market share of more than 20%.
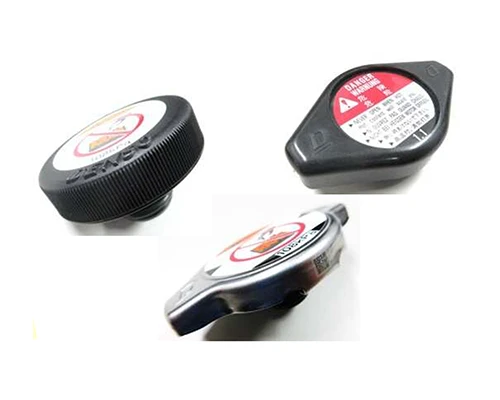
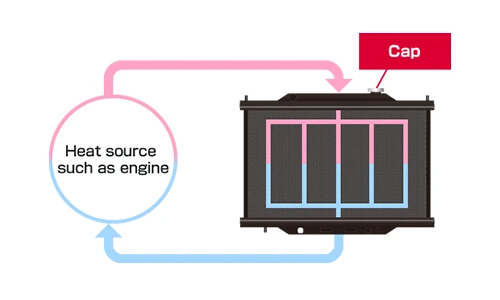
What is a radiator cap?
The radiator cap is a cover (cap) of the radiator, which cools down coolant at a high temperature in the mobility.
However, its role extends beyond being a cap for preventing coolant leakage. It is an important component part that prevents overheating of the engine by maintaining the proper pressure in the radiator with the spring inside the cap.
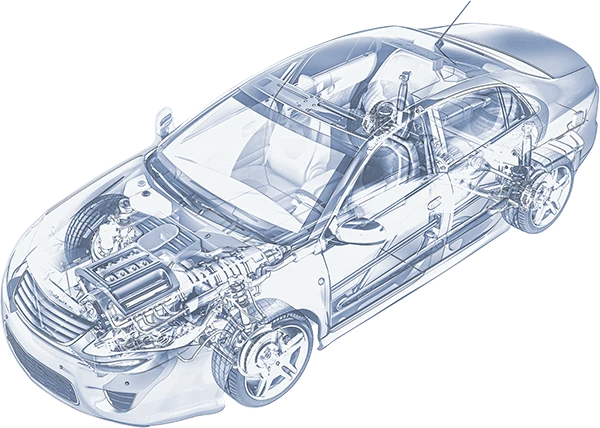
At Nippa, we continue to grow with the manufacturing of essential components in mobility, particularly focusing on radiator caps as our main business. Currently, we take pride in a domestic market share exceeding 70% and an overseas share of over 20%. With a track record of introducing our products to various industry customers, we refine our technology by leveraging our experience and know-how. Through this ongoing improvement, we provide our customers with trust as a top manufacturer and offer one-of-a-kind value.
Nippa’s cap manufacturing carrier
Nippa has been manufacturing radiator caps since 1955, and has accumulated know-how and technology over many years. We manufacture a wide variety of caps such as M, L-CAP, S-CAP, and N-CAP.
Install in various vehicles
Many customers have selected caps manufactured by our company.
2 wheels
4 wheels
Large vehicle
Agricultural construction machinery
Other EVs
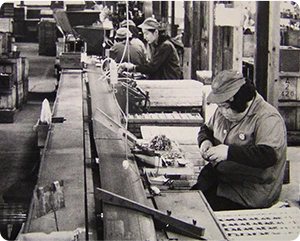
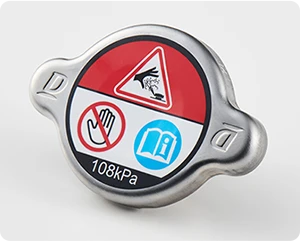
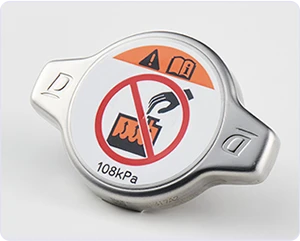
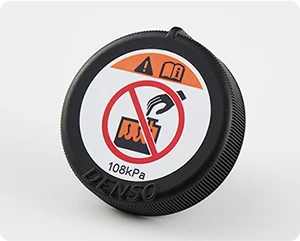
Nippa's cap assembly4 strengths
Integrated production system
By consistently handling everything from part processing to assemble and inspection in-house, it enables efficient and smart manufacturing without waste.
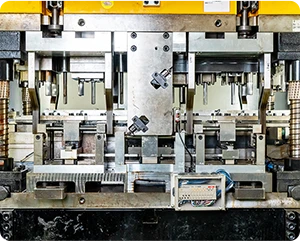
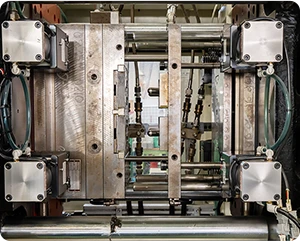
Stamping and resin molding
All of the stamped and resin parts that make up the cap are produced in-house.
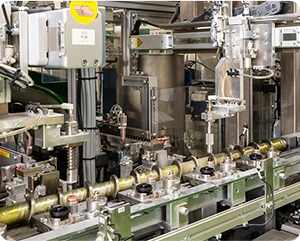
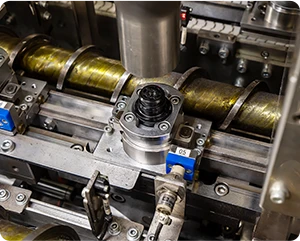
Automated assembly
In assembly lines with parts that have various sizes and shapes, we perform automatic processes from part supply to processing.
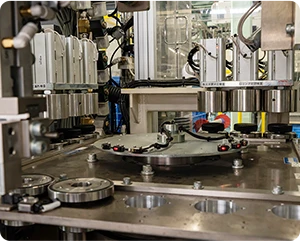
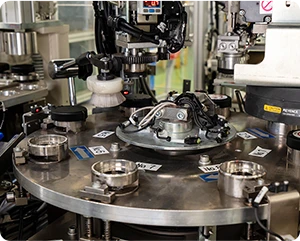
Automated Inspection
We achieve full assurance by building a mechanism for automatic inspection system tailored to product requirements.
Cultivated Technological Capabilities
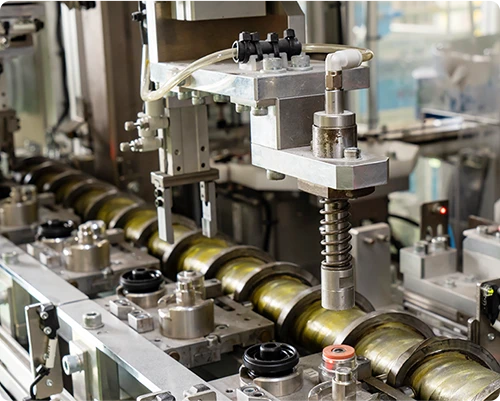
As a long-established manufacturer of cap manufacturing, we have continually realized various assembly requests, leading to the development and possession of a wide range of assembly technologies. Leveraging the technology we have cultivated over many years, we strive to meet customer needs closely and propose/provide products that bring greater satisfaction.
Furthermore, by actively pursuing automation through machinery, we have achieved the automation of the entire process from parts supply to processing and inspection. The cycle time has been reduced, enabling mass production and allowing flexible adaptation to changes in market demand. In recent years, we have introduced lots to improve line efficiency and visualized CHOKOTEI (line stops due to primary issues) to enhance productivity.
-
Stopper fastening
-
Spot welding(N-cap)
-
Ultrasonic welding(Resin screw cap)
-
Labeling
Inspection/quality control capabilities
By consistently handling everything from the part production and assembly to inspection in-house, it enables efficient and smart manufacturing without waste.
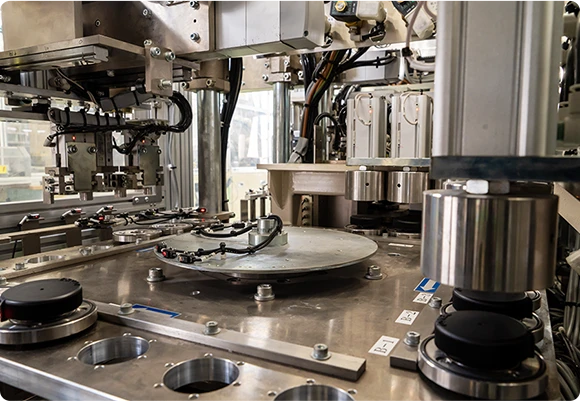
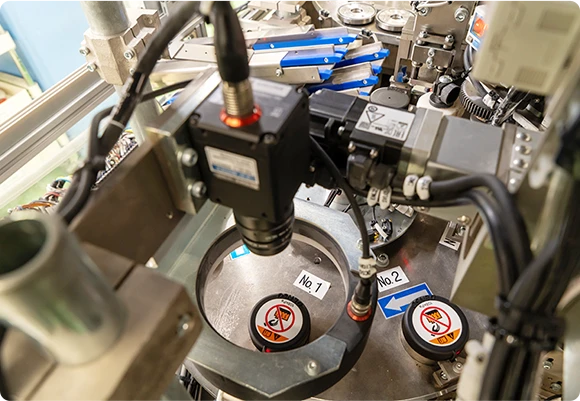
On-site capabilities
Initiatives at the head office factoryMetal cap manufacturing team
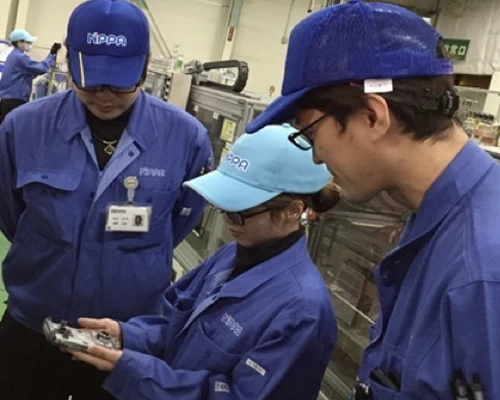
The Production Section plays a leading role in on-site improvement.
To consistently maintain a high operational rate on the production line, we prioritize 'Quick Action,' and simple repairs and adjustments are carried out within the production department. Additionally, for challenging issues, we collaborate with the technical and equipment maintenance departments based on information gathered by the production section, working together with professionals in each field to address and resolve issues.
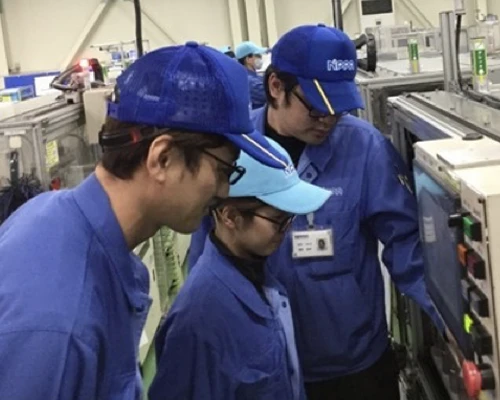
Value the equipment with care
In the factory, there are machines that have been in operation for more than 30 years. To ensure the safe and accurate use of these long-operating machines, it is crucial for the on-site personnel to keenly observe daily minor changes. By checking for abnormalities and differences in actuator movements that deviate from normal conditions on a daily basis, we can prevent malfunctions in advance. This proactive approach has enabled these machines to continue their active role, even after several decades of operation.
Initiatives at the Iwata factoryResin screw cap manufacturing team
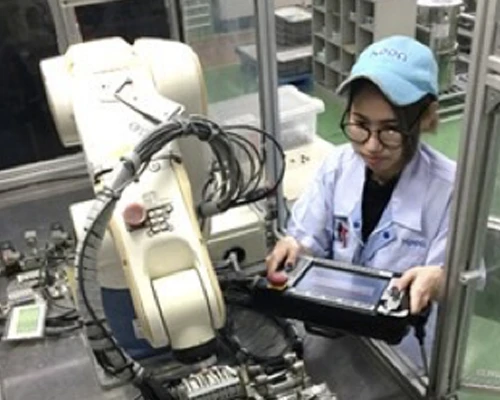
Each and every person is a doctor for equipment
In our workplace, adjustments and repairs of equipments are carried out by the operators themselves. By conducting them on the production site, the equipments are consistently kept in optimal condition, allowing us to maintain high operational efficiency. To achieve this, we place a strong emphasis on firstly “understanding the facilities well = knowing what is normal”. Employees on the field take pride in having an in-depth understanding of the equipments they are responsible for, believing that they know it 'better than anyone else,' as they are the ones who can save it.
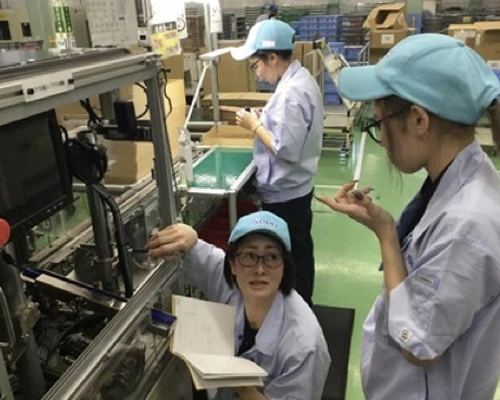
Cheerful site environment
As one of the principles guiding our daily production activities at Nippa, we consciously strive to 'enjoy our work.' Even in small matters, by reaching out to each other, communication is fostered, leading to increased exchange of opinions between individuals. When facing issues on site, , active exchange of opinions gives birth to ideas, leading to problem solutions. We believe that creating a cheerful work environment contributes to better product development.